Alternating Current Field Measurement (ACFM) is an advanced electromagnetic testing technique originally developed for offshore applications. Today, ACFM is widely used across numerous industries for the detection and sizing of surface-breaking cracks in welds, coatings, and metallic structures — without requiring surface removal.
The technique is recognized by both ASME and EN standards, and it allows for large, uninterrupted scan areas through the use of software markers that accurately locate and size indications in real time.
Benefits of ACFM:
- Detects and sizes surface-breaking cracks without coating removal
- Accurately determines through-wall crack height
- Enables inspection of painted or coated surfaces, saving time and cost
- Minimizes the need for surface grinding or prep
- Suitable for in-service inspection, even in difficult-to-access areas
- Offers data logging and traceability through electronic record-keeping
AFCM Applications:
- Power Industry: Inspection of tank farms, deaerator heaters, storage tanks, HEP piping systems, valve bodies, and hydroelectric stations (e.g., draft tubes and spiral casing welds)
- Petrochemical: Ideal for coke drum cracking inspections and minimizing grinding during routine internal assessments
- Amusement & Leisure Parks: Monitoring of welds on high-speed rides and complex structural programs
- Tank Storage Facilities: Internal/external inspection of circumferential seams and nozzles without removing protective coatings
- Cargo Cranes & Lifting Equipment: Frequently used for weld surveys due to minimal prep and high sizing accuracy
- Other Applications: Bridges, stadium structures, railway tracks, and large-scale civil infrastructure
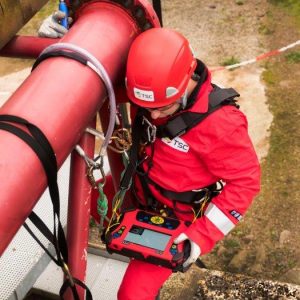
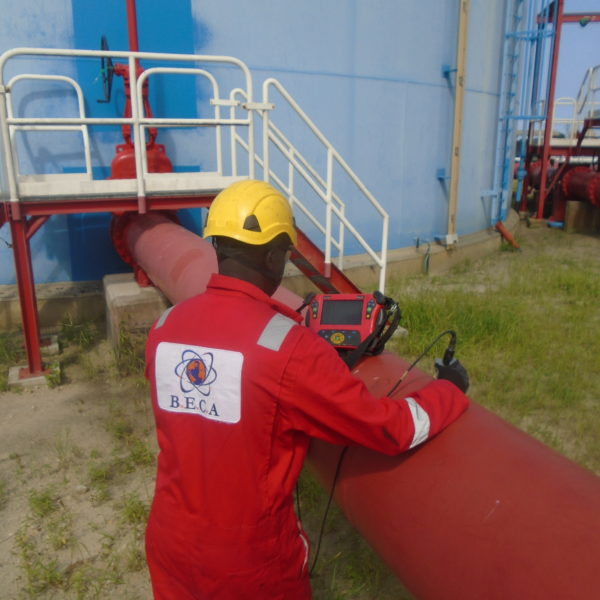
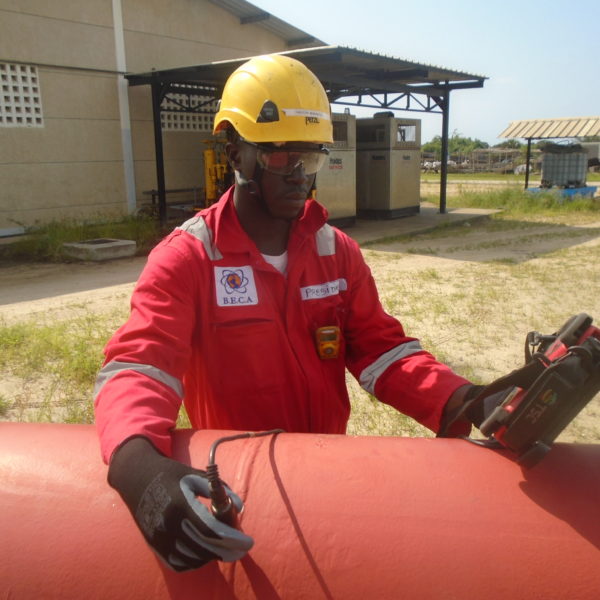
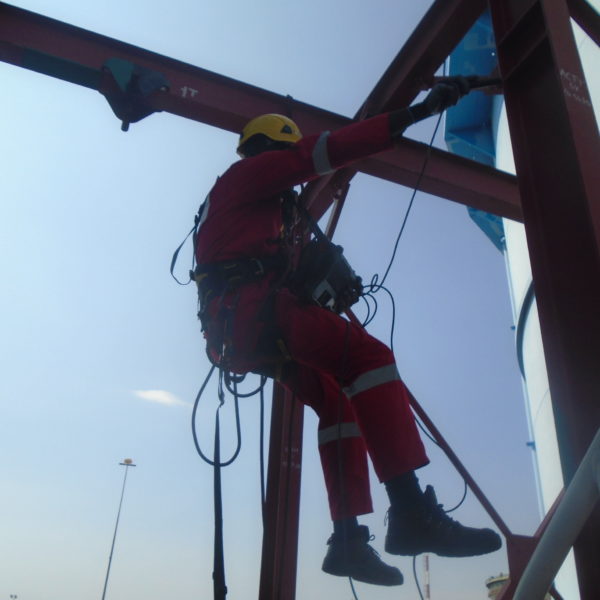
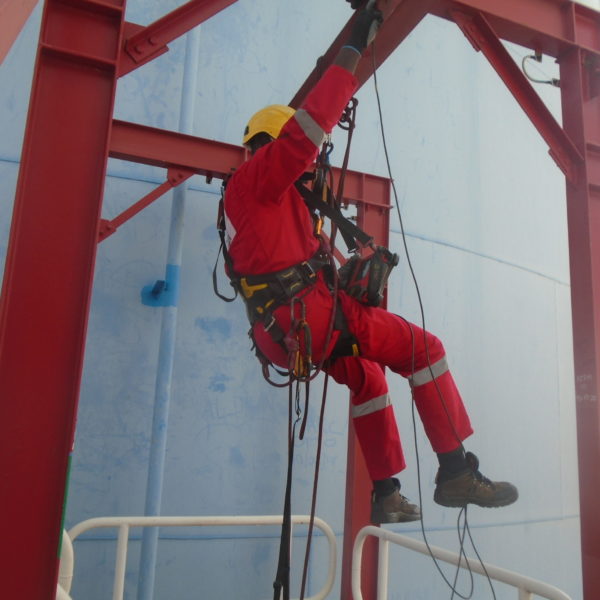
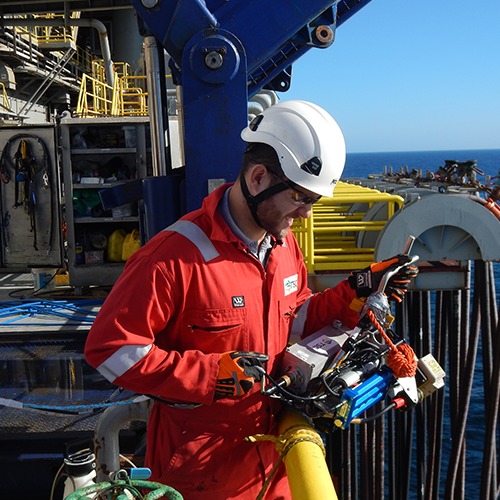